“截至目前,我们利用3D打印技术修复综采工作面刮板输送机链轮环、转载机链轮环共计74件。”神华神东煤炭集团设备管理中心三机大修项目主管张宏庆说,“利用3D打印技术修复的链轮环,使用性能和寿命达到新件水平,但同购买新件相比,成本大幅降低了。”
为啥用3D打印技术修复煤机部件
2014年以前,神东煤炭集团少数齿面磨损不严重的链轮环利用传统补焊工艺修复,而磨损相对严重的链轮环只能报废。
“看着堆积成山的报废链轮环,大家很苦恼。一方面是心疼钱,另一方面是觉得当前修复技术这么先进,却不能解决这个小问题,或多或少有些不服气。”张宏庆说。
那几年,正值3D打印技术逐步成熟,铺天盖地的宣传报道引起了大家的注意。该技术广泛应用于航空材料、医疗装备、精密仪器等方面,在煤机部件修复领域鲜有涉及。
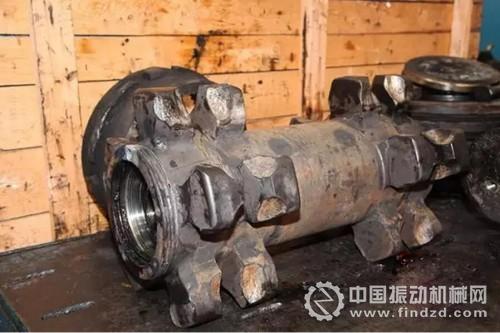
张宏庆说,当时的争论很大,有些人觉得,设备坏了,采用传统补焊工艺可以简单修复,再不行的话可以买新的,何必多此一举呢?况且3D打印技术能不能运用到煤机部件修复上?使用后效果怎么样……这些问题让大家有些犹豫。
“要做就做第一家,要做就一定要做好”,神东煤炭集团领导的支持让大家彻底放下了包袱。
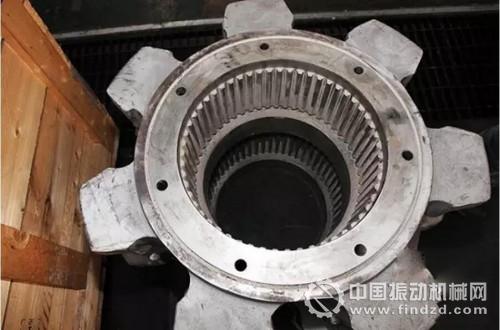
经过前期调研比对,神东煤炭集团最终决定与西安一家3D打印技术公司合作。在做了测绘、取样对比、数据论证等大量准备工作后,技术人员开始试着对链轮环进行修复。
笔者了解到,神东煤炭集团采用的是激光立体成形技术,它属于3D打印技术的一种。
激光立体成形技术结合了快速原型技术和激光熔覆技术,是以实现高性能复杂结构金属零件无模具、快速和全致密近净成形为目的的先进制造技术。与传统的加工方法相比,激光立体成形技术不再需要刀具、夹具和机床就可以打造出任意形状,且其强度和塑性可达到锻件水平,为解决设备维修部件的高性能直接成形和快速修复问题提供了一条技术路径。
根据部件三维模型数据,应用激光立体成形技术能让材料逐点、逐线、逐层堆积,快速而准确地制造出部件,这是一种“增材”制造方法。
正是这种“增材”制造方法,让神东煤炭集团维修人员眼前一亮。经过半年试用,针对利用3D打印技术修复的链轮环崩齿、磨损过快等问题,技术人员合理调整了修复工艺及打印粉末配比,在修复区域形状和部件缺损形状吻合度上进行了细化。
2014年6月,利用3D打印技术修复煤机部件的条件基本成熟,神东煤炭集团开始推广应用。
修复后的煤机部件使用寿命达到新件水平
链轮环长期与链条相互配合,在巨大冲击力作用下,链轮环齿面极易磨损、断裂,一般采用传统氩弧焊补焊工艺对其进行修复,但需使用耐磨焊条对链轮环进行补焊、上数控铣床铣出配套链条齿、对齿面进行淬火处理等。
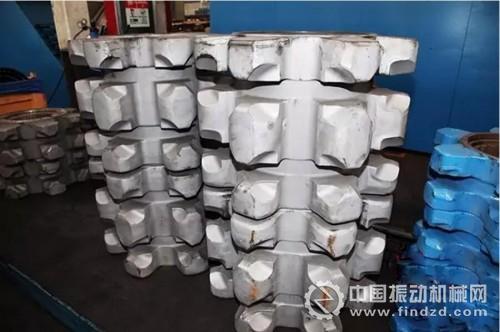
传统工艺工序繁琐,焊后需进行机械加工等,效率低且修复后需热处理才能达到使用要求,外观比较粗糙,且只能对磨损量小于20毫米的部件进行修复,超过这个尺度的链轮环只能报废处理,而利用3D打印技术修复链轮环可以完全消除传统氩弧焊补焊工艺的弊端。
利用3D打印技术修复链轮环的步骤是这样的:链轮环修复前,维修人员先对链轮环进行清理及编号,这是一种“身份登记”。随后,三维扫描仪开始对链轮环进行扫描并形成点云数据,激光立体成形数据处理软件根据数据确定修补区域,并计算修补区域差值。这一过程包括三维模型打开、三维模型变换与观察、三维模型剖分、剖分路径修改、路径填充、填充路径修改与优化、数控代码生成等步骤,等这些工作做完后,真正的“增材”工作开始。
维修人员只需将待修复链轮环放至合适位置,激光3D打印机立即开始自动修复。维修人员将这个过程形象地比喻为“头重脚轻”,即前期准备时间长,而真正修复很简单。
据张宏庆介绍,利用3D打印技术修复煤机部件的前提是建立庞大的部件原型数据库,这依托于一系列软硬件,需要对新采购的部件在入库前利用三坐标测量仪进行详细测量,测量数据的精度直接关系到后期修复部件的尺寸精度。而修复后的部件需在井下工况环境下进行试用,并根据试用情况对修复工艺及粉末进行调整。
“在修复过程中,激光束方向、能量可控性好,这对精确确定修复区域、最大限度减少链轮环变形大有好处。待修复区域与链轮环本体处为致密冶金结合,不易导致复体脱落、剥离。修复区域形状和部件缺损形状接近,表面质量高,不需后期加工,一次成形,而且整个过程由计算机控制,可靠性、重复性强,更美观。”张宏庆说,“修复后的链轮环实际使用寿命基本能够达到新件水平,成本更低。”
据了解,神东煤炭集团利用3D打印技术修复的74件链轮环,如果全部采购新链轮环需要1200万元,但利用3D打印技术修复链轮环只需要670万元,节约530万元。
目前,神东煤炭集团确定了包括综采机、连采机、掘锚机、泵站等在内的7大类共计121项利用3D打印技术修复的部件,部分部件已经进入试修试用阶段,等到评议合格后即可批量修复。