12月5日15时20分,河钢矿业司家营北区分公司选矿二厂1#5585溢流型球磨机成功恢复运转。自10月27日至今1个多月的时间,球磨机大齿轮异常开裂严重影响了生产。从拆卸补焊,到催发备件,再到昼夜赶工安装,职工们历经数十个昼夜的不眠不休,终于换得了球磨机的正常运转。
“ 加班补焊 未有一丝一毫松懈起初,球磨机大齿轮上出现一道“油渍”,但屡次擦拭都未能将其清除,岗位工立即意识到是设备本身出了问题,随后经逐级上报并开始组织抢修。由于球磨机的大齿轮并非易损部件,因此并没有列入日常备件计划范畴,而厂家生产这样的一个部件最短也要6个月的时间,“补焊修复”成为解决问题的唯一途径。
10月27日,大齿轮修复战役正式打响。在球磨机设备厂家技术人员的指导下,该选厂开始对大齿圈进行拆卸补焊。焊接的过程十分繁琐,要经过气刨、打磨、加热、焊接、再加热、缓冷、打磨、探伤等多道程序,为了抢抓时间,焊接过程始终是昼夜赶工,严防死守每一个工作细节。期间,抢修人员一边进行修复治理,一边密切关注大齿轮拆装后的变形情况。11月4日晚,首次焊接工作结束,抢修人员正准备迎接成功的喜悦,却不料进行螺丝紧固时发现焊接点再次开裂。突发问题让已奋战十天的抢修工作陷入了僵局,但备件“遥遥无期”,多番思量过后他们选择进行再次尝试。
随后又是一个十余天的不眠不休以及重复的焊接作业,期间抢修人员结合实际情况多次调整焊接方案,更换焊丝、调整加热温度及保温时间等等,为了控制齿轮变形量,还特意在焊接部位加装了加固筋板,同时为了减小球磨机负荷,试车前进行了“减球”操作,将球磨机筒体内的钢球减少至原来的三分之一。11月17日凌晨1点,安装精度检测合格的球磨机迎来了第二次试车操作,此次焊接处未见开裂,却发现齿轮出现了异响,起初技术人员以为是齿轮啮合的接触面不合理造成了转动过程中的异响,抢修人员继续进行“研齿”操作,进一步测试安装精度,以求找到异响的症结所在,然而两日后再次试车时却发现异响仍未消除……此时,所有的办法已用尽,虽已历经二十余天的不懈努力,但不得不面对一个现实问题:简单的补焊修复已不足以解决当前的严峻问题。尽管补焊未能使问题得到解决,但是公司进行了“两手准备”,在进行补焊工作的同时公司各级部门积极与厂家联系,以使球磨机尽快恢复运转为根本出发点,加紧协调备件问题,加快督促备件到货,终于12月2日晚上9点,大齿轮备件抵达现场。
“ 昼夜安装 用行动赢取时间为了尽可能节省安装时间,早在备件到货前该分公司积极论证大齿轮安装方案,并结合备件的到货时间于12月1日前对旧齿轮进行拆除,为即将到来的新齿轮安装做好万全准备。
备件到货后,严阵以待的检修人员按部就班的对所有的齿面和安装表面进行彻底的打磨清理,特别是将大齿轮剖分面、大齿轮与筒体结合面所有的毛刺和磕碰伤一一消除殆尽。处理完所有安装前准备事宜,12月3日凌晨1点,开始了第一个半齿轮的吊装工作,由于齿轮直径长约8.43 米,重余48吨,而齿轮啮合对吊装精确度要求较高,因此需要天车工和指挥人员毫厘不差的默契配合。只见吊装现场,两根等长的吊绳从两边套穿在半齿轮轮辐的空档内,为防止吊绳损伤齿轮,吊绳与大齿轮之间还额外增加了防护垫,将第一个半齿轮起吊后扣在筒体上方,使上下齿根处尽量对齐,大齿轮与筒体螺栓孔基本对好以后,检修人员开始穿入全部螺栓,每隔三个螺栓适力进行一次紧固,随后通过调整螺栓来微调大齿轮的位置。待第一个半齿轮吊装完成时已时近凌晨6点,检修人员“马不停蹄”开始进行第二个半齿轮的拆卸安装作业。先用慢驱盘车将下一半齿圈转到上面,使半齿圈把合面处于水平位置,随后将旧齿轮拆卸,按装配标记安装第二个半齿轮。
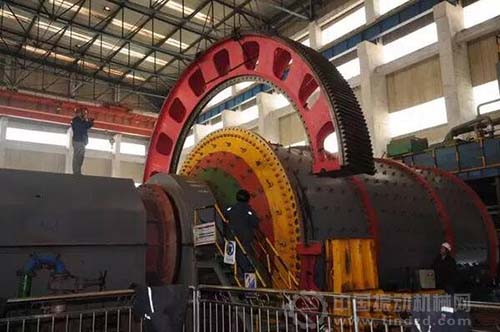
图为球磨机大齿轮吊装现场
12月3日上午10点,记者赶到现场时,恰逢第二个半齿轮安装作业的进行时,现场作业紧张中不失慌乱,半齿轮自起吊至到位的吊装时间不过几分钟,却让现场每一个人绷紧了心弦,天车指挥人员站在醒目位置,一声哨响后,随着他精确的手势,半齿圈开始脱离地面或左或右或上或下的缓缓移动,特别是最后关头吊装操作更为谨慎,待两边半齿轮对接口处以定位哑铃销精确对准后,现场人员无一不松了一口气,开始进行下一步操作。在全体检修人员争分夺秒的紧密配合下,当日晚24点基本完成了两个齿轮的安装作业。
“ 精细调整 球磨机恢复了运转大齿轮吊装作业结束后,真正的挑战才刚刚开始,大齿轮的找正调整以及大小齿轮的侧隙把控实为此次安装作业的“重头戏”。早在安装之前,检修人员便被告知新齿轮相对旧齿轮尺寸偏小,因此要做到和原球磨机的“严丝合缝”还需费上一番功夫。
两个半齿轮把合好后,拧上全部大齿轮和端盖的连接螺栓,检修人员开始利用大齿轮径向调整螺栓调整齿圈径向位置,大齿轮径向跳动是安装精度的主要考核指标,为了使大齿轮径向跳动不超过2mm,检修人员将大齿轮的轮齿等分为12个点,在大齿轮的轮缘面涂写标记,并用千分表在大齿轮外圆两侧30mm范围的找正带上打表找正径向跳动,繁琐的操作流程在经验娴熟的检修人员手中却显得“轻车熟路”。大齿轮径向跳动满足要求后,并没有宣告调整结束,而是按照安装方案进行大齿轮径跳复查,测量大齿轮端面的轴向摆动,慢慢旋转大齿轮,记下每一测点的三个读数,直至大齿轮旋转一周,“千分表的指针回零,误差小于0.1mm,径向跳动满足要求”,做完了这十分关键的一个步骤,副主任郭宝文欣喜的宣布了这一结果。调整所有跳动符合要求后,将所有螺栓全部拧紧,记录最终的径向和轴向跳动,各项指标全部符合要求。至此大齿轮的安装调试已成功了大半。
待大齿轮找正后,检修人员开始测量安装作业的另一关键指标——大小齿轮侧隙,“9.2mm,比正常值高出了近一半”,这一结果检修人员早有预料,新齿轮尺寸比旧齿轮偏小,势必会出现这样的难题,好在在此之前已想好了应对之策:移动球磨机筒体。暂停了二系列球磨,取出其中的球磨顶起装置,清理1#球磨机两侧大瓦座周围油污,并去除限位块,利用四个千斤顶把1#球磨筒体顶起5mm左右,随后用顶丝调整筒体,落下顶起装置,测量齿侧隙,再顶起调整,如此反复操作,直到间隙满足了要求。12月5日的下午14时,所有的安装作业已经精细调整终于宣布结束,随后经过简单的后期处理,15时20分,球磨机终于成功转车。
打赢了安装之战并未让一线的职工放松了警惕,在随后的指标调试期,他们坚持将谨慎与认真做到极致,密切关注试运转期间球磨机的每一丝动向,密切跟踪球磨指标变化,竭尽全力确保其快速投入正常使用。