“劳动强度低了,工作效率高了;人员减少了,回煤生产工效高了;设备堵卡事故率少了,操作简易方便了;自动化程度高了,装车轻松便捷了。”山东能源枣矿集团蒋庄煤矿智能化选煤厂在持续推进过程中不断散发出“青春活力”。
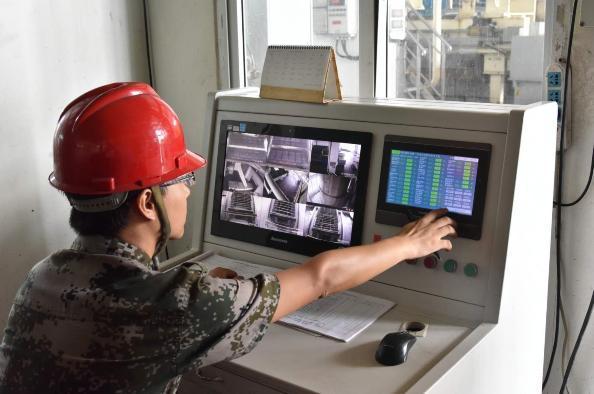
蒋庄煤矿选煤厂持续提升装备水平和自主创新能力,坚持用人最少、效率最高、效益最优工作思路,不断优化、完善各生产系统,力促设备提档升级,逐步向全面智能化不断推进。“过去一台压滤机只有70块滤板,现在换了新装备,滤板增加到105块,处理能力提升了50%,产量由过去的4.5t/循环提升至6.75t/循环,单机日处理量提升85t,极大的缓解煤泥水处理压力,职工劳动强度大大降低。”该厂洗煤车间主任王义春说。原来,选煤厂针对原压滤设备老化、工艺落后、洗选效率低等制约生产的“瓶颈”问题,对原使用的压滤设备进行了更换升级,新型设备自动化循环卸料实现了压滤机智能控制,职工从岗位操作工转变为巡检工,生产效率提高了25%。在洗煤压滤车间有着10年工作经验的压滤工张萍,提起压滤机的更换升级,对其称赞滔滔不绝。“在整个压滤机卸料过程中,我们原来需要人工2个人配合卸料,频繁开停设备,劳动强度非常大,20分钟完成后全身都湿透了。如果再遇到煤泥水喷料的情况,现场环境和安全系数更是不可保证。现在我们只需要1个人轻轻按下按钮,在不靠近设备的情况下5分钟便可独立完成卸料,环境变美了,而且安全也有了可靠的保证。”张萍开心的说道。
他们还对回优化升级,先后安装使用了齿辊筛、破碎机以及除铁器。“回煤系统的升级改造,彻底解决了外来煤超粒度问题,减少设备堵卡事故率,入洗原煤符合重介分选工艺要求,提高了回煤生产工效,降低职工劳动强度。”该厂装运车间主任孟祥龙说。针对原来渣浆泵入料中容易进入超粒度颗粒,极易造成堵塞的问题,他们设计制作了渣浆泵除杂装置。该装置通过底部放料阀门,让超粒度颗粒自流卸出,如有超大颗粒物料,可拆卸上部端盖,提出箅网,清除杂物,防止对泵体内部结构造成破坏。“为彻底解决浓缩机压耗事故不易被发现的状况,我们通过技术创新改造,在浓缩机上自行设计安装了浓缩机停耙报警装置。”选煤厂机电技术员张建说。据张建介绍,耙式浓缩机是选煤厂煤泥水处理的主要设备,在停止运行的时候,一旦发现不及时,事故会从停耙事故向压耙事故恶性转变,增加维修处理难度和劳动强度,严重影响洗煤生产的正常运行。目前,该装置已投入使用,当浓缩机运行停止,接近开关检测的信号时间差超过设定值,操作室的报警灯就会亮起,调度员可以很直观的观察到报警信息,以便及时通知人员对现场设备进行维修处理,避免了生产事故发生,提高了设备的运转率,具有较好的推广、应用价值。“今年以来,我们不断提高装备水平、优化生产系统和劳动组织,先后对大型设备进行投入安装使用,并通过创新改造,先后完成了浮选远程定量加药、块矸远程放仓、地销装车远程控制等一系列自动化系统改造,提高了生产能力和工作效率,降低了职工的劳动强度。”该厂厂长褚衍静说。
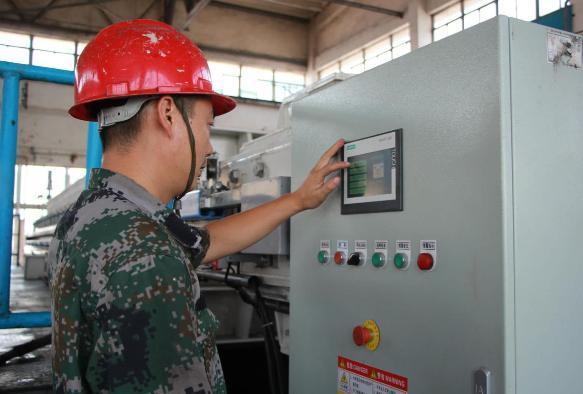
在此基础上汽车装车及压车系统进行了智能化升级改造,该装置利用皮带和伸缩溜槽装载、压实一次完成,工作人员仅需动动手指进行“一键启动”操作即可节省人力和操作时间,装车速度由原来的100吨/小时提高到目前的600吨/小时,原来人工装车至少需要2部铲车8人轮流操作,现在只需3人即可完成所有工作,解决了精煤直接落地的难题,提高了设备自动化程度、安全系数和装车效率,为地销精煤装车外运带来极大便捷。并通过封闭式装车,消除了煤尘污染现象。
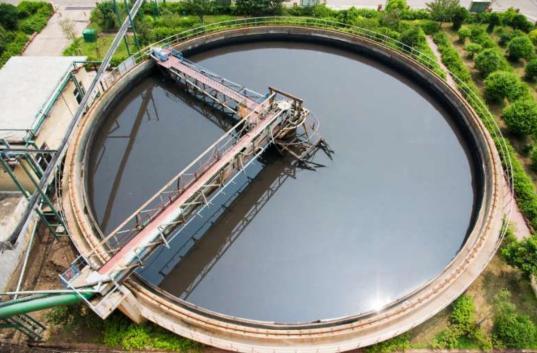
与此同时,他们秉承“小投入、大成效”的理念,投入136万元进行自动控制系统升级改造,实现了生产系统“一键启停”和全流程自动化控制,可通过视频监控画面查看到设备启动情况。设备在“一键启动”时,集控界面上设备颜色将发生变化,能直观显示设备开启流程,达到了控员提效目的,洗煤生产人员有原170人减至45人,年节约人工成本近千万元。今年以来,蒋庄煤矿以智能化选煤厂创建为目标,通过实施装备升级、生产调度集中控制、远程视频监控等手段,精简优化岗位近20个,通过“机械化换人,自动化减人”,实现了控员提效、精干高效。