由于选矿流程设备多、工况复杂,依靠传统手段实现原料成分、工艺参数、设备状态和产品质量在线检测难度很大,这些严重制约着选矿流程的精细化控制和资源能源的高效利用。近日,记者在金川集团股份有限公司(以下简称金川集团)了解到,金川集团选矿厂利用5G+、AI视觉分析、机器人及智能算法技术,打造了破碎—磨矿—浮选全流程的“数字基础设施集成”场景,统筹推进选矿数实融合,加快传统机械化装备向自动化装备更新。此前,金川集团选矿厂的“数字基础设施集成”场景入选了2023年度智能制造优秀场景名单。
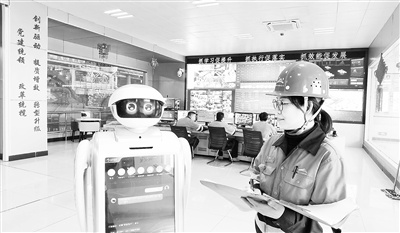
岗位职工向智能巡检机器人下达指令。 金川集团新闻中心供图
近年来,全球矿山资源由“高品位、易选别矿种”逐步向“低品位、难处理、多组分共伴生复杂矿为主”转变。这导致了选矿流程长、资源综合利用率低、生产成本高等问题,也成为阻碍相关企业结构转型升级和高质量发展的瓶颈。为解决矿山企业资源高效利用问题,金川集团选矿厂基于选矿工艺的信息化和智能化需求,逐步完成了生产过程中多项应用场景的建设,实现了选矿流程主要工序生产指标、关键装备、人机安全的一体化智能管控。
通过工艺建模、流程仿真、数字化交付等信息化技术,金川集团选矿厂建立了破碎筛分和磨矿分级工艺模型,搭建智能稳定给料场景。“场景的落地不仅打破了碎矿和磨矿工艺参数人工测量、手工调整的历史,还首次实现了多工序协同控制、参数动态优化和物料平衡,使磨矿可选粒级提高10%以上。”金川集团一选矿车间碎矿生产运行班副班长张金胜说。
针对全区域、各岗位的不同监控需求,金川集团选矿厂基于在线点检及故障诊断系统搭建设备智能管控场景,增加轨道机器人对浮选设备运行状态和电机温度进行实时监测,实现了在主控室和移动端随时可以查看设备故障诊断与预知性维护信息。由此,设备故障率每年降低约15%。金川集团一选矿车间设备技术员张志扬介绍:“设备智能管控场景通过5G+操控无人化,实现了碎矿全系统‘一键启停’式集中控制,以及原矿段、中细碎段和筛分段的连锁保护、连锁启停。我们在控制系统中组态设置关键设备、关键测点三区变量和设备运行状态,实现了关键参数的预警和报警。”
应用5G+技术,金川集团选矿厂对底层数据、应用数据进行采集、筛选,将生产运行、设备状态、安全管控、能源消耗等数据建立成统一数据库,构建数据智能分析与分层管控、故障自动报警、信息查询和检索、数据定期推送等集成化管理,并将集成后的相关数据作为生产信息化管理的指导依据。在“数字基础设施集成”场景下,2023年,金川集团选矿厂各工序、系统达到了高满负荷协同作业,全厂系统作业率达到90.7%,部分系统负荷率达到103%,处理矿量达到1250万吨,同比增加5.84%;镍回收率完成84.43%,高于计划0.13%,铜回收率完成78.53%,高于计划1.03%。
“在数字化选矿建设的道路上,我们积极探索并取得初步效果。但选矿数字化底座还需持续夯实,工艺数据的价值还需深度挖掘,数据治理还任重道远。”金川集团选矿厂厂长谢杰说。