2013年6月19日,由中国煤炭加工利用协会选煤分会组织的“全国洗煤厂节能降耗、挖潜提效技术研讨会”在湖北省襄阳市隆重召开,冀中能源峰峰集团马头洗选厂生产副厂长兼总工程师周娟华、重介车间副主任王文元参会。该厂介耗从投产时的6kg/t原煤降低到现如今的0.41kg/t原煤,刷新不脱泥不分级全重介选煤厂的介耗管理全国纪录,其经验得到了与会专家领导的关注。
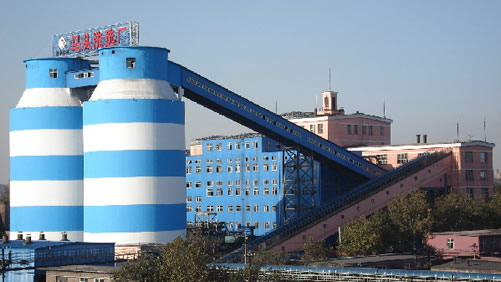
马头洗选厂是华北地区最大的主焦煤选煤厂,现生产工艺为不脱泥无压给料三产品全重介+直接浮选工艺,年入洗原煤能力1000万吨以上,下设马头总厂、九龙分厂和孙庄分厂。其中马头总厂是“一五”期间由前苏联援建的国家156项重点工程之一。
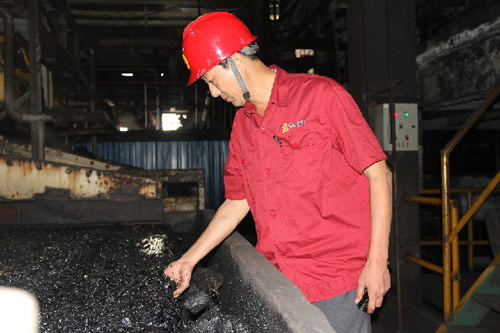
近年来,马头洗选厂大胆解放思想,坚持创新驱动,抢抓机遇发展,始终将科技思维和科技手段贯穿于企业发展的各个领域、各个环节。该厂以市场需求作为创新路标,以行业高端作为奋斗目标,围绕降低重介质消耗这一选煤厂主要经济技术指标,进行了一系列大胆探索与实践,使重介质消耗指标不断降低,2012年,马选厂介耗达到了全年0.5 Kg/t原煤以下。2013年4月份又创历史新低,达到了0.41Kg/t原煤的国内同行业领先水平。经测算,按照2012年入洗原煤煤432万吨,介耗按0.41 kg/t原煤计算,介质粉价格按1000元/t计算,预计每年可节约介质686.88吨,增加经济效益686.88万元。
思想是破解难题的动力和源泉。2009年,该厂把介耗降至并稳定在2kg/t原煤以下。但此后的降介耗活动便遭遇了瓶颈期,降介耗成效一直难有突破。面对困境,该厂组织工程技术人员,对2010年元月份生产介耗展开分析,通过对技术损失和管理损失两方面的调研论证,一致认为还有一定的潜力可以挖掘。为最大限度降低介耗,该厂在坚持好弧形筛定期倒头更换、磁选机入料均质化、脱介筛喷头清理等常规工作的同时,还从优化工艺、转变理念、技术创新和精细管理四方面入手,进行了大胆探索与实践。
马头洗选厂入洗原煤中<0.5mm粒级煤泥含量在25%左右,个别批次原煤煤泥含量达到30%以上。该厂原设计中有煤泥重介分选工艺,作为中央型选煤厂,入洗原煤的煤泥量与原煤性质和原煤处理量相关,有着极大的波动性,这就导致分流量的适时调整与煤泥重介所要求的稳定分流量产生了矛盾,影响到分选效果。同时重介质悬浮液系统也随之产生波动,极不稳定。通过生产实践数据检测,该厂在2010年去除了煤泥重介分选工艺。工艺系统仍保留煤泥重介桶及泵,并增加磁选机入料分料箱,来均衡各精煤磁选机的入料量,保证稳定给料。
洗煤厂的生产管理,不单纯是运转设备的管理,而是在动态的煤泥水系统平衡中实现各种产品分离的过程控制。介耗管理必须放在整个系统中,树立全局观念,才能真正把介质消耗降低下来。这一颠覆传统操作理念的想法和举动,稳定了选煤作业流程。
基于上述认识,马头洗选厂在组织生产过程中,围绕煤泥水系统的量(最适宜的流量)和质(各个环节中煤泥水的浓度),从有效的调控入浮浓度入手,将流量稳定在一定的范围内。这样保持了各产物的桶位平衡,保持了煤泥水系统中煤泥量的相对稳定。这对于马头洗选厂这样入洗矿别多、煤种差别大的中央型选煤厂而言,是一个十分重要的理念转变。原煤处理量应根据煤质作相应的调整,马选厂在生产实践中,根据不同的入洗矿别,摸索出适宜的处理量,将浮选入浮量控制在1800m3/h左右、入浮浓度控制在100-120g/l后,浮选作业和煤泥水系统可以提供持续稳定的优质清水,而将重介系统也可将分流量控制在一定的范围内,保证了磁选机入料的数量和质量的相对稳定,合介桶位的平衡易于控制,从而为重介选煤系统创造了稳定的生产大环境。
持此之外,马头洗选厂坚持创新驱动,持续推进了9项科技改造,增强了降耗核心动力。为提高脱介筛喷水压力、增加精煤磁选机。由于马选入洗原煤为焦煤,煤泥发粘,在通常的0.12-0.15Mpa喷水压力下,产品带介量较高。通过调整系统的水量,将压力控制0.18-0.20Mpa之间。喷水压力提高后,脱介筛喷水量随之提高,因此又增加了两台精煤磁选机来保证其通过量。实施了扩大精煤、中煤定压箱改造。原设计精煤、中煤定压箱与悬浮液出料管距离太近,不能对悬浮液形成很好的缓冲。将精煤、中煤定压箱进行扩大改造后,使得从旋流器出来的悬浮液能够以自流形式进入弧形筛,从而保证了弧形筛入料均匀。旋流器精煤溢流分料箱加设可移动插板。马选两个生产系统中共有七台精煤脱介筛,分料不均直接导致产品带介。如何将精煤脱介筛分料均匀,一直是介耗管理的重点。通过摸索在精煤分料箱上加设可移动插板,根据生产中四台精煤脱介筛的分量大小进行实时调节,保证各台精煤脱介筛分料均匀。弧形筛包角改造。充分利用弧形筛的循环回收作用是保证介耗的前提,将弧形筛包角调试到最佳角度才能最大限度的发挥好弧形筛的脱介作用。经现场多次验证分析,弧形筛包角在60度时,弧形筛利用面积最大,脱介效率最高。脱介筛第一道喷水闸门电动集中控制。脱介筛第一道喷水直接进入原煤合介桶,人工手动闸门控制速度慢,会导致开停车过程中大量循环水进入原煤合介桶,稀释悬浮液。悬浮液稀释后,需通过打分流将水排出,既提高了磁选尾矿带介,又延长了开车后加煤时间。脱介筛第一道喷水闸门施行电动控制后,大大降低了循环水进入原煤合介桶,降低了生产介耗和电耗。增加脱介筛喷水边缘喷头。脱介筛喷头安装过程中,各脱介筛边缘不同程度的都存在有喷水盲区,使得脱介筛边缘产品带介较多。通过增设脱介筛喷水管边缘喷头,并将边缘喷头进行倾斜安装,杜绝了脱介筛喷水盲区,降低了产品带介。中煤脱介筛一段底流改造。中煤脱介筛由于悬浮液循环量大,弧形筛磨损较快,在连续开车更换不及时的情况下,很容易导致中煤产品大量带介。将中煤脱介筛第一段底流由走磁选机改为走原煤合介桶,在弧形筛脱介效果变差的前提下,通过脱介筛第一道筛板将其继续回收,既降低了中煤产品带介,又延长了弧形筛使用寿命。矸石弧形筛定压箱内加稀释水。矸石磁选机入料中,虽然煤泥含量少,但由于旋流器的浓缩作用,矸石产物中带介量比较大,马选厂工艺选型中,矸石脱介筛和磁选机都比中煤的偏小,增加喷水,会导致磁选机入料量过大,为此,在矸石弧形筛定压箱内增加喷水,来进行稀释,而不加重后续作业负担。磁选机喷水改造。原设计中磁选机采用胶皮将粘附在磁选机滚筒上的介质刮掉,但生产中根本无法刮净,导致粘附在磁选机滚筒上的介质随磁选尾矿流失。将胶皮改为喷水后,大大降低了磁选机磁选机滚筒上介质随磁选尾矿的流失,降低了磁选尾矿带介。
马头洗选厂领导班子认为,机制是破解难题的车轮和保证。工艺系统成熟稳定后,需要有良好的管理去维护。马头洗洗厂细分管理环节目标,量化考核精细管理,将精细化管理思想渗透到介耗管理的方方面面。
他们制定了对标考核制度。介耗对标考核制度是由班后分析、每旬排名、月度奖惩组成的三位一体考核制度,从点到面、全程管理。当班介耗超过1kg/t原煤,车间值班领导、班组长和介耗相关岗位人员班后必须进行分析,查找原因、落实责任;每旬对各班介耗完成情况进行对标排名,要求落后班组提出整改措施;每月对介耗完成较好班组给予一定奖励,对落后班组联挂考核。树立内部和外部标杆,不断自我激励、自我完善,从制度上促使职工降介耗工作自觉化、常态化。
严格了四级巡检制度。四级巡检制度是由车间管理人员、班长、一级巡检员、岗位巡检员组成的四个层级的巡检制度。要求管理人员每班不定期、班长每班至少一次、一级巡检员每班至少两次、岗位司机每小时一次对设备运转状况、产品和磁选尾矿带介、喷水压力等进行层层巡查,有效杜绝了生产中的跑、冒、滴、漏现象,产品带介或磁选尾矿带介后能够得到及时解决,保证了生产过程中介耗指标不失控。
细化了编码定置管理。对脱介筛、磁选机、筛板、喷头等进行编码定置管理,既便于相互交流,又能形成对重点设备、重点环节的的重点关注。巡检中对堵塞的喷头进行记录,停车后进行重点处理;停车后,对各筛板尺寸进行测量,大于0.5mm筛缝超过50%时立即更换。编码定置管理有效杜绝了设备隐患,保证设备良好运转。
制定了协同奖惩制度。介耗受多种因素的影响,其指标完成需要重介车间全时间、全方位的带介检查,需要浮选车间对喷水压力和循环水质的良好控制,需要机电科对介耗设备的有效维护,需要质检科严把介质粉质量关,需要调度室对生产开停车和事故过程中的协调指挥,任何一个环节出现问题,都会导致介耗偏高。为此,马选厂制定出了严格明细的协同奖惩制度,及时找出问题症结,落实相关责任单位,为各单位之间的密切有效配合提供了制度保障。