1新矿集团龙固选煤厂属矿井型重介选煤厂,设计生产能力6Mt/a。选煤工艺为:原煤分级后,块煤进入动筛跳汰机进行分选,处理后的产品进入破碎机进行破碎,破碎机排出粒度要求小于50mm,再经混料泵输送至两产品重介旋流器进行进一步分选处理。
2精煤破碎机的选择
FP系列强力分级破碎机主要利用剪切力和拉力的作用对物料进行破碎,其转速较低,一般为70~75r/min,齿形特殊,可破碎抗压强度达120MPa。其主要工作部件为2个平行安装的齿辊,每个齿辊沿轴向布置一定数量的齿环,当物料进入破碎机双辊之间,即被辊子上的鹰嘴形齿咬住,并逐渐增大施加的压力,靠低速剪切或拉伸来破碎物料,且冲击能量较小。破碎齿呈人字形螺旋排列,将物料自动向两边分开,像旋转的格筛一样将符合粒度要求的物料从间隙直接排出,且在齿尖后部设有11°~12°的排料角,确保物料能迅速从扩展空间排出,从而增大了处理量,防止物料的过粉碎。破碎后的产品粒度均匀,超粒与过粉碎均较少,适合煤炭物料的破碎。
因此确定该厂选用型号为FP5020GB的FP系列强力破碎机,其主要技术参数:
入料粒度/mm:≤300
排料粒度为/mm:≤50
齿辊间距/mm:500
破碎强度/MPa:≤120
生产能力/t·h-1:210~280
电动机功率/kW:110
电压/V:660
3现场超粒问题调研和影响因素分析
(1) 现场超粒问题调研该厂的精煤破碎机用于最终破碎,破碎后的产品进入洗选系统的两产品重介旋流器进行分选。根据工艺系统要求,对超粒的要求非常严格,超粒后系统会产生很大的波动,但对破碎机产生的过粉碎要求不高。在实际生产过程中出现大块矸石造成破碎机堵转停机,洗选系统出现管路堵塞致使无法生产,堵塞的位置为混料泵的流道,该位置直径为准92mm。对破碎后进入工艺系统的产品进行粒度组成分析,发现大于50mm的物料约占30%,超粒问题严重,易造成系统堵塞,超粒的物料粒度大多处于60~70mm,极少部分大于85mm,当2个较大的块煤搭接在一起时,就有可能造成泵的堵塞。
(2) 影响超粒的因素分析
① 破碎机入料粒度超粒严重对进入破碎机前的物料和破碎后的物料进行对比分析,发现进入破碎机的物料中存在大块矸石,最大粒度达到600mm。破碎机入料前级设备为动筛跳汰机,当系统出现超粒或动筛跳汰机排矸性能不好时,排出物料含有块矸较多,现场发现有大量的矸石进入破碎机,造成破碎机堵转停机,由于矸石硬度高,破碎机的排料出现严重的超粒现象;
② 矿井原煤粒度组成不稳定,进入洗选系统物料超粒严重由于煤矿井下未设置破碎站,原煤未经过处理直接提升,粒度难以控制,原煤储煤场使用固定钢篦子控制最大粒度,实际效果并不好,出现条状超粒现象,发现进入破碎机的粒度最大500mm,大于破碎机要求的入料粒度(小于300mm)。由于原煤粒度和矸石含量都较大,造成破碎机性能下降,排料超粒严重。
4改进措施
根据现场实际情况,制定改进措施:
(1) 控制原煤入洗的粒度根据入洗的原煤实际情况,发现矿井提升的原煤超粒现象严重,井下需要增加1台大型破碎机,将原煤粒度破碎到300mm以下,达到选煤厂要求粒度后,再进入洗选系统进行洗选。同时将原煤储煤场固定钢篦子空隙尺寸由原来的300mm×300mm调整为260mm×260mm,减少大块原煤进入洗选系统;
(2) 调整破碎机的齿辊转速提高破碎机齿辊的转速,加大破碎齿对物料的冲击破碎作用,尽量减少排料超粒现象。通过变频器调节,对破碎机的齿辊转速进行控制;
(3) 改进破碎机的齿形,减小包容空间所谓包容空间是指两破碎辊齿在旋转中,齿面相互配合形成的封闭空间,一般来说,块精煤的韧性较差,该空间可大一些,这样可以增加物料的通过性。但是从破碎后的块煤上很容易发现有破碎齿的划痕,说明原煤中块煤韧性好、不易破碎。针对以上情况,减小破碎机的包容空间,具体措施:在破碎机每个齿环根部一周采用耐磨合金焊条堆焊合金高约20mm,减小齿形的包容空间,同时在齿窝处堆焊直径准20mm、高20mm的小齿,减小齿窝的容纳空间。包容空间处理措施如图1所示。
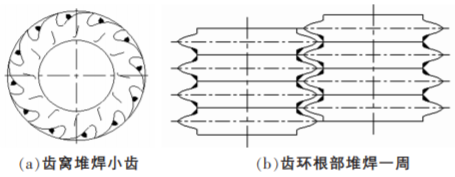
图1 包容空间处理措施
5改进后效果分析
破碎机经过转速调整和齿形处理后,超粒现象大为改观,经现场对破碎前后采样分析,得到破碎机入料和排料粒度组成和粒度组成曲线分别如表1和图2所示。
表1 破碎机入料和排料粒度组成
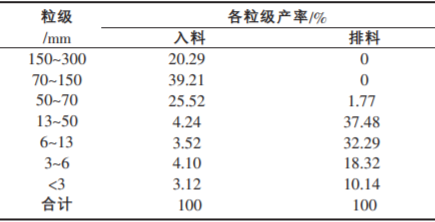
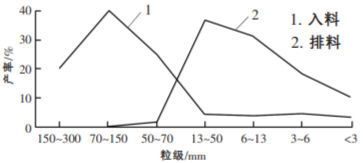
图2 粒度组成曲线
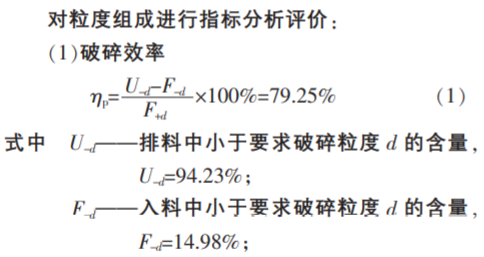
式(3)中取1.2倍要求的破碎粒度为最大限制粒度,主要是考虑系统对粒度尺寸有一定的包容度。
从表1看出,超粒率ψ=1.77%,超粒现象得到明显的改善,在正常的偏差范围内。通过本次改进,超粒问题得到了很好的解决。
6结语
通过龙固选煤厂精煤破碎机的选择以及解决使用过程中出现的超粒现象,探讨了对超粒的影响因素,采取多项改进措施,超粒问题得到了很好的解决,对类似选煤厂破碎机的选择和超粒问题的处理有指导和借鉴意义。