原料厂烧结车间成品筛分系统,是根据生产需要将经热破和冷却后的烧结矿,利用振动筛将不同粒级的烧结矿分选出来,是烧结生产过程最重要的环节之一。整粒的好坏直接影响到成品烧结矿的粒度组成,影响到返矿和铺底料的质量,进而影响到高炉正常生产。
传统的烧结筛,在结构上存在一定的缺陷,出现故障时需启动备用设备,倒链板机机头翻板进行倒筛作业。长期以来,倒筛作业时需停链板机,进入机头溜槽内进行割焊作业,不仅危险系数大,倒翻板降料层外翻生产设备故障率也高。另外后期倒运外翻料工作量大,影响生产的同时也增加了员工劳动强度。
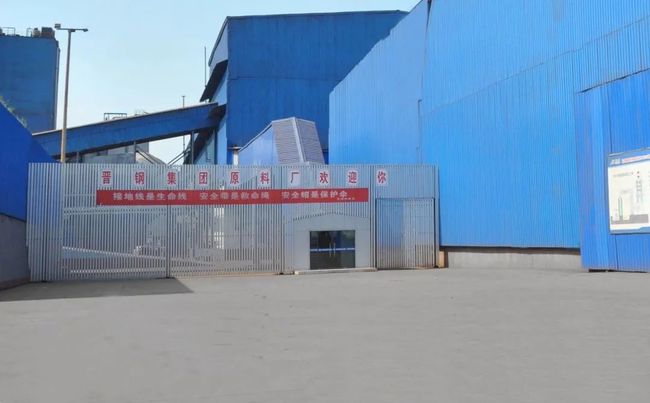
为解决这一难题,晋钢集团维修技术骨干从优化生产工艺入手决定对损坏的筛分系统进行维护改造。经多次现场研模调试,利用检修时间将链板机下料口溜槽旧翻板割除,调整溜槽角度至合适状态,在下料口处制作密封罩和支架,成功解决了倒翻板需人工调试、耗时长的弊端。改造后倒筛作业,只需将其中一条线的链板机下料口堵满,料会自动流向另一个溜槽,与之前的倒翻板作用一致。
改造实施后,筛分系统倒筛既不用停链板机,也不用降料层外翻生产,节省了大量的人力物力财力,为成品系统的生产顺行起到了很大的促进作用。